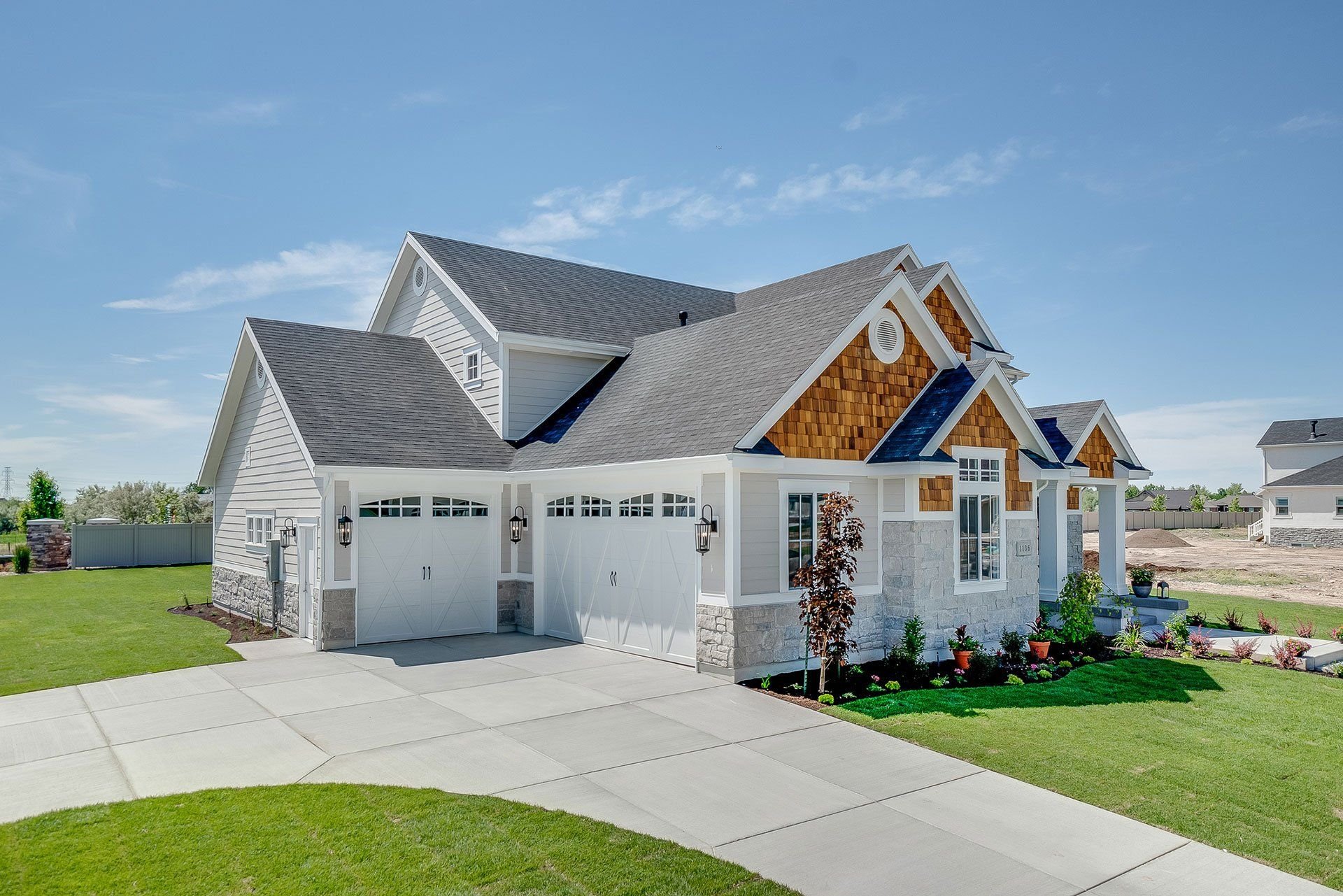
Raleigh’s Most Trusted Roofing Company
TPO
What is TPO Roofing?
TPO Roofing (Thermoplastic Olefin roofing), is a single-ply roofing membrane commonly used in commercial and industrial buildings. It is known for its durability, energy efficiency and cost-effectiveness.
TPO roofing is made up of a blend of polypropylene and ethylene-propylene rubber, which gives it excellent resistance to UV radiation, heat and chemical damage. This type of roofing is typically white or light-colored, which helps to reflect sunlight and reduce energy consumption for cooling purposes.
TPO membrane is manufactured in large sheets (10,12 or 20 feet wide). They are heat-welded together at the seams to create a seamless and watertight barrier. Its lightweight nature makes it relatively easy to install, and it requires minimal maintenance over its lifespan.
It's worth noting that TPO roofing has gained popularity in recent years as a sustainable roofing option due to its recyclability and energy-saving properties. Many businesses and building owners opt for TPO roofing to enhance their energy efficiency and reduce their environmental impact.
TPO Roofing Installation Process:
1. Roof Inspection: Before installing TPO roofing, a thorough inspection of the existing roof is conducted to identify any underlying issues or damage that needs to be addressed.
2. Roof Preparation: The roof surface is cleaned and prepared to ensure proper adhesion of the TPO membrane. This may involve removing any debris, repairing damaged areas, and applying a suitable primer.
3. Attachment of Insulation: If insulation is required, it is installed on the roof surface first. This helps to improve energy efficiency and provide additional thermal protection.
4. Membrane Installation: TPO roofing is typically installed in large, prefabricated sheets. These sheets are rolled out onto the roof surface and positioned, ensuring proper alignment and overlap.
5. Heat Welding: Once the sheets are in place, the seams and edges are heat welded together using specialized equipment. This process creates a strong, watertight bond between the TPO membrane sheets.
6. Flashing Installation: Flashing is installed around roof penetrations, such as chimneys, vents, and skylights, to provide additional waterproofing protection. Flashing materials compatible with TPO roofing are used for this purpose.
7. Final Touches: After the TPO membrane and flashing are installed, any necessary finishing touches are completed. This may involve trimming excess material, ensuring proper drainage, and inspecting for any imperfections.
Advantages and Disadvantages of TPO Roofing:
Advantages:
1. Durability: TPO roofing is known for its durability and resistance to punctures, tears, and impact damage. It can withstand harsh weather conditions, including high winds and hail.
2. Energy Efficiency: TPO roofing is typically white or light-colored, which helps to reflect sunlight and reduce heat absorption. This can lead to lower cooling costs and increased energy efficiency.
3. Cost-Effective: TPO roofing is generally more affordable compared to other roofing materials, such as PVC or EPDM. It offers good value for the price, making it a popular choice for commercial and industrial buildings.
4. Easy Installation: TPO roofing comes in large sheets that are heat-welded together, creating a seamless and watertight membrane. This installation method is relatively quick and straightforward, saving both time and labor costs.
5. Environmentally Friendly: TPO roofing is considered a sustainable roofing option due to its recyclability. It can be recycled at the end of its lifespan, reducing environmental impact.
Disadvantages:
1. Longevity: While TPO roofing is durable, it may not have the same lifespan as other roofing materials like PVC or metal. The exact lifespan can vary depending on factors such as climate, maintenance, and installation quality.
2. Susceptible to Chemical Damage: TPO roofing may be vulnerable to certain chemical substances, such as oils and greases. If exposed to these substances, it can lead to degradation and reduced performance.
3. Limited Color Options: TPO roofing is primarily available in white or light-colored options. While this can be advantageous for energy efficiency, it may not provide as much flexibility in terms of aesthetic choices.
4. Quality Variations: The quality of TPO roofing can vary among manufacturers. It's important to choose a reputable brand and ensure the product meets industry standards to ensure long-term performance.
5. Maintenance Requirements: While TPO roofing requires minimal maintenance, it still benefits from periodic inspections and upkeep. Regular cleaning and inspections for any damage or issues are recommended to prolong its lifespan.
It's worth noting that the pros and cons can vary depending on specific factors such as climate, installation quality, and maintenance practices. Consulting with a roofing professional can help determine if TPO roofing is the right choice for your specific needs.
HOW TO REPAIR A TPO ROOF?
The lifespan of a TPO roof is typically around 15-20 years. However, over time, issues like seam damage, flashing failures, and punctures can occur, leading to roof leaks. The presence of water inside the building is usually the first indication that a TPO roof requires repair. This occurs when the seams lose their adhesion, allowing water to penetrate the roofing insulation.
When the insulation becomes saturated with water, it eventually seeps into the roofing deck and starts causing leaks inside the building. At this point, it is crucial to contact a professional commercial roofing contractor to conduct a thorough roofing inspection.
During the inspection, the contractor will assess various factors including:
- Identifying the points of water entry into the insulation
- Determining the age of the TPO roof
- Evaluating the number of roof layers
- Assessing the condition of the seams
Based on the findings of the inspection, the building owner can explore different repair options. For instance, if the roof is 12 years old and the seams are slightly uplifted, immediate action is necessary. Neglecting the repairs will result in further separation of the seams with every gust of wind, leading to more water infiltration into the insulation.
To determine the extent of insulation saturation, a roofing contractor may perform an infrared inspection. This involves visiting the roof about 30 minutes after sunset when the roof's surface is cooler than the water-saturated insulation.
Using an infrared camera, the contractor can detect temperature differences and mark the areas requiring attention with spray paint.
REPAIR OPTIONS FOR TPO ROOFS WITH LESS THAN 25% SATURATION
Following a comprehensive infrared survey, if it is determined that your roof has less than 25% saturation, there are repair options available, such as a silicone restoration membrane system.
The installation process for a silicone restoration membrane system involves:
1. Removal and replacement of saturated areas with similar materials.
2. Power washing and thorough cleaning of the entire field of the roof.
3. Strengthening and reinforcing the seams of the TPO roof.
4. Application of silicone coating to the entire roof surface.
5. Granting of a new 10-20-year warranty.
In another situation, even if the saturation is below 25%, the condition of the seams may be too deteriorated for restoration using a silicone system.
In such cases, if there is only one roofing system, one option is to install a cover board over the TPO roof, remove the flashings, and then apply a spray foam roofing system. This approach can help save costs compared to a complete tear-off and installation of a new TPO system.
However, if you already have two roofing layers and the seams are in poor condition, the best course of action would be to remove all the TPO and install a new roofing system.
REPAIR OPTIONS FOR TPO ROOFS WITH MORE THAN 25% SATURATION
Following the thorough infrared inspection, if it is determined that the roof has excessive saturation, a silicone restoration membrane system may not be a viable solution. In such cases, an alternative approach is necessary.
Unfortunately, the only viable choice in this situation is to remove all the TPO and insulation, exposing the roofing deck. This provides an opportunity to install a new roofing system, and given the previous issues, it may be advantageous to consider a different option.
One recommended alternative is a spray foam roofing system. Here are some reasons why it could be a suitable choice:
1. Exceptional insulation properties: Spray foam boasts the highest R-value per inch of thickness among all roofing systems.
2. Renewability: After 10-20 years, the roof can be recoated to maintain the warranty, which is a more cost-effective option compared to a complete tear-off.
3. Seamless protection: Spray foam forms a seamless layer, eliminating common areas where leaks tend to occur.
4. Easy installation: Spray foam roofing systems are known for their ease of installation.
In the case of a TPO roof that requires a tear-off, a spray foam roofing contractor would typically install a cover board and then apply the spray foam over it.
It is crucial to understand that the extent of saturation determines the available repair options. If the saturation exceeds 25%, a complete tear-off is necessary to remove all the wet insulation. However, if the saturation is below 25%, there are more repair choices available.
It is always cost-effective to address repairs at an early stage before they cause extensive damage.